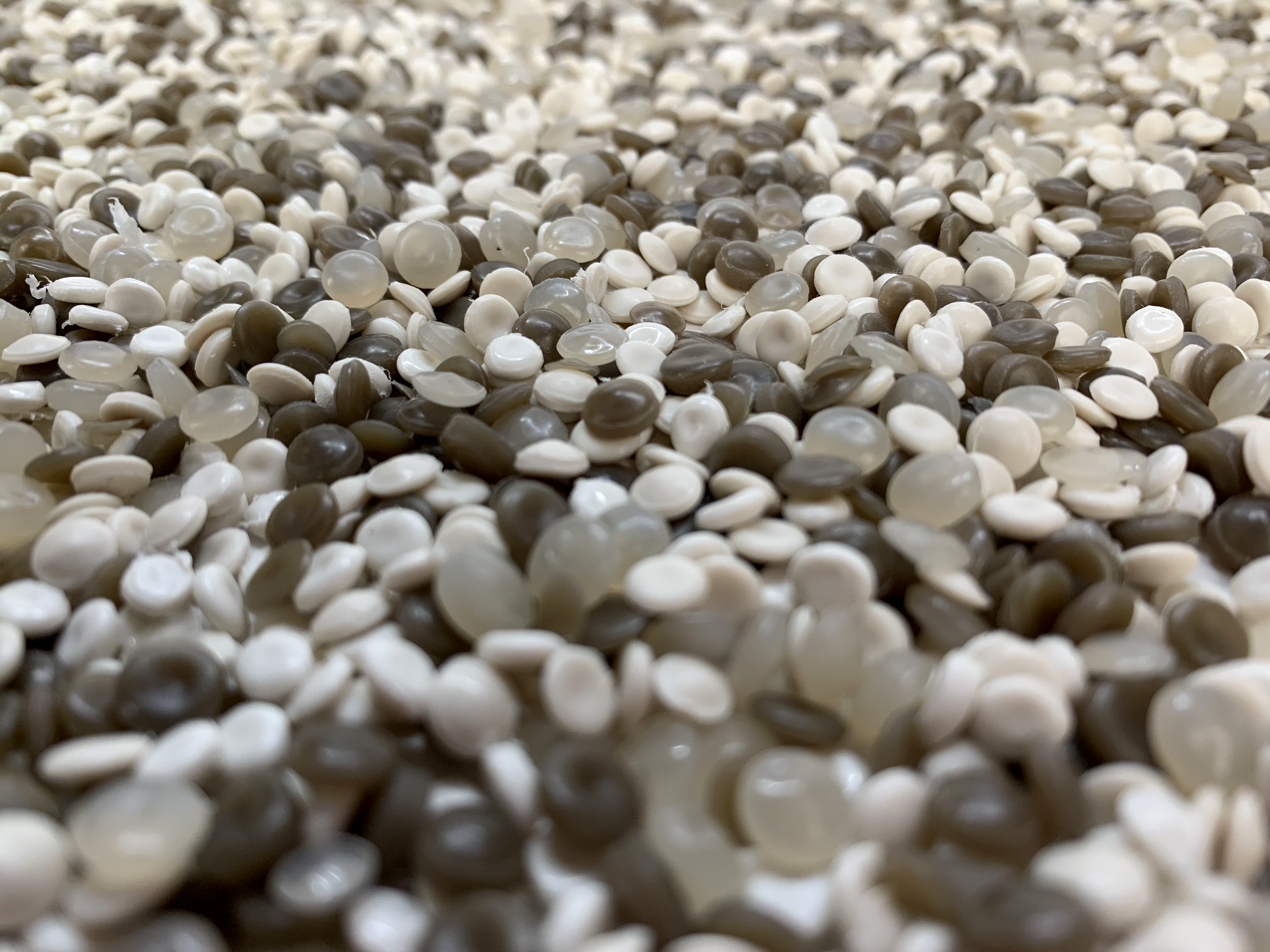
Are you thinking about incorporating Post-Consumer Recycled (PCR) resins into your flexible film products? The world is demanding that we address the issue of plastic waste (can add an impactful reference here such as “According to Greenpeace, the volume of the packaging material used by the e-commerce sector was 9.4 million tons in 2019, and it is expected to reach 41.3 million tons by 2025. Also, about 850,000 metric ton of plastic waste was produced by the package-delivery sector in 2018”).
If you make flexible polyethylene films, an obvious way to reduce plastic waste is to use PCR resin in your products. This might feel like a challenge for a number of reasons.
- Film production is not forgiving, and waste plastics can be inconsistent and contain too many
contaminates.
- There are not many options in the market for PCR de signed for film conversion in terms of melt index and cleanliness
- PE films are notoriously competitive in terms of price and performance
Before you embark on this worthy journey, we want you to know more about PCR
#1 – How is Post-Consumer (PCR) different from Post-Industrial Recycled (PIR), repro, and wide spec plastic resins?
Post-consumer recycled is defined as having served its purpose; after the product’s intended use in the market, it is collected, processed, cleaned and repelletized into PCR resin. When plastic is transformed into a product, then lost in manufacturing due to change over, overruns, and mistakes, it can be reprocessed back into a resin format. However, since it never served its intended use by cus tomers, it is considered Post-industrial recycled resin.
PIR can typically be used back in the original process and is less likely to end up in a landfill. Repro is short for “Reprocessed”. This is a plasticmade mostly from post-industrial parts that are ground into small format and then pelletized. The transformation of the plastic into a part has made the resin unusable back in the original product.
And finally, wide spec resin is not a recycled product. It is a virgin resin that has not been trans formed in any way. Wide spec generally consists of resin that is out of specification or has a perfor mance range wider than the intended specification.
Reducing plastic waste in our environment requires the use of materials that are most likely to be disposed in landfills and do so on a continuous and substantial way. Use of wide spec does not reduce plastic waste at all and PIR waste streams can often be used back into the source product – making PIR simply good manufacturing practice. Repro consumption keeps plastic waste out of landfills; however, supply is often variable and uncertain. This leaves PCR as the best solution when your goal is to formulate a product that incorporates recycle. Predictable supply and manageable consistency gives you the abil ity and the confidence to make a recycle based product that can then be marketed for its positive environmental impact.
#2 What specifications (e.g. MFI, density, etc.) should I expect from PCR resins?
The melt index, melt flow ratio, and density are basic properties that should be communicated on every lot of PCR. We offer some observations that will make your experience with PCR align better with expectations. While PCR rheology curves may look similar to virgin resins, it is important to un derstand the shear thinning behavior and melt strength of the resin during processing. For instance, if LDPE is present in a LLDPE based PCR, the resin will process as if it has a higher MFI than indicat ed. Care should also be given to selecting a PCR based on density values only. Mineral fillers are of ten present which can make the density will appear to be higher than the actual base polymer density. Ash is a good property to evaluate along with density.
#3 What can I expect in term of processability of PCR resins?
Melt Flow Ratio is a good indicator for processability – a higher number indicates it will be easier to process. Also, it is important to align the source of PCR to your final product and processing needs – if your process requires a melt index of 2 or above, it is ideal to find a PCR to suit your needs rather than try to work with a fractional melt that will make processing difficult and frustrating. Resin suppli ers have a role to play here as well, as PCR can be provided as a melt compounded blend with virgin resin to alleviate issues such as MI mismatch.
#4 What impact on film performance should I expect when using PCR resin?
Since PCR is often used as a blend component, it is important to understand how the PCR properties will affect your overall perfor mance. The first step in using a PCR blend is to compare the phys ical property performance of PCR to a virgin resin. Make sure you choose the right resin to conduct a fair comparison – try to align the MI and density of the PCR to your comparative virgin resin. Physical property retention can be quite good provided the PCR is high qual ity and free of contamination. If performance falls short, consider changing to a higher performance virgin resin in the blend to over come the slight reduction in performance.
Exploring how much PCR to use in your product design is key in applications development and should be done on a case by case basis. The level of PCR content often depends on cleanliness (gels or impurities), physical property retention, and desired aesthet ics. For cleanliness and gel level, ask your supplier about their cleaning steps and their melt filtration capabilities. For physical property retention, matching density is important and if this is not possible consider what can be done to offset the resulting change in performance. With regards to aesthetics, our advice is to embrace the ugly! PCR is not likely to look as good as virgin, even if the utmost care is taken in its production. Let the different aesthetic start telling the story for the consumer to understand that PCR is being used in your product design – the sustainability messaging is a key component to driving growth in the circu lar economy!
#5 What else should I watch out for in using PCR resin?
You should ask your PCR supplier if any additives have been added, such as slip or blocking agents. These additives can have a negative impact on your product performance. Anti-blocking agents can interfere with tackiness required for stretch films for instance. There are beneficial additives that you also want to ask about. Antioxidants may improve PCR stability and film performance. If you think the PCR needs stabilization, collaborate with your resin supplier.
Most plastic manufacturers can attest that PCR often has a different odor compared to virgin plastic. Good PCR suppliers address odor early in the recycling process. It is critical to remove paper labels and cellulosic/organic contamination in the wash step to prevent particles from charring during the ex trusion process. Devolatilization and deodorizing additives are secondary activities that can improve perceived odors. Ask your supplier if any of these steps are included in their process.
Finally, if you have a special criterion such as absence declarations and food contact, work with your supplier to address these needs. The FDA has a specific process defined to achieve a letter of Non Objection (LNO), which is one criterion for food contact. PCR should not be used for food contact applica-tions unless it has explicit statements indicating that it is safe to do so – an LNO is only one piece of the entire picture.